Mejor proyecto Fin de Grado en Ingeniería en Organización Industrial
JUAN CARLOS GIETZ
ALBERTO DE LA CALLE
Director del proyecto
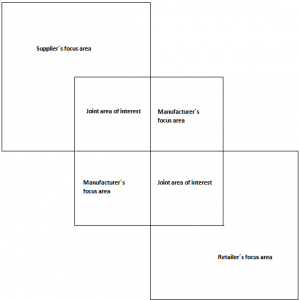
of Interest
Motivation
The new and changing requirements of demand consolidate the supply chain management study as an area of growing interest. Indeed, it has turned out that the Supply Chain (hereafter SC) can become an exceedingly powerful competitive advantage for any industrial organization. As stated by many authors, current competition does not take place between mere enterprises any longer but rather between whole supply chains, from its first supplier to the end consumer.
Problem
However, in all existing Supply Chain networks, the flow of information both upstream and downstream deteriorates the further it gets transmitted from one echelon to the next one in the chain due to demand forecasting errors, poor communication, mistrust among the members of the chain, etc. Consequently,
the Bullwhip Effect appears. The fluctuations in clients demand may usually have a harmful effect on the whole system because of the high level of existing interdependence among the echelons. Hence,
high variable replenishment orders will certainly flawed forecasts while simultaneously the inventories at each level of the SC will be insufficient provided, precluding them to afford possible demand peaks.
The consequences can be defined on the one hand as an unlimited growth of the warehouse´s inventory resulting in increasing inventory costs, and on the other, increased backlogged orders due to stock shortages.
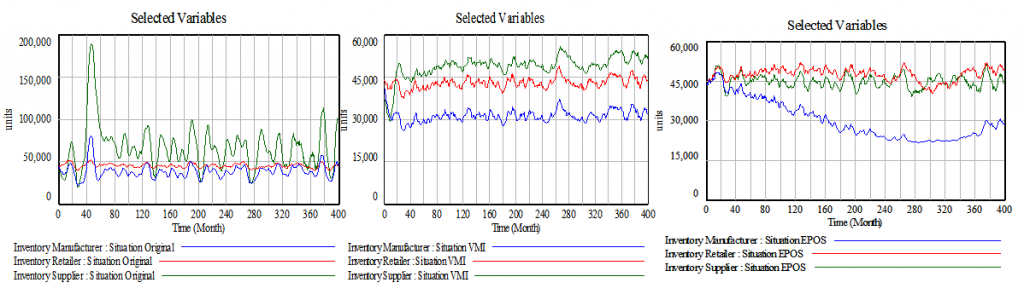
Objective
The project is based upon the revision of previous experiences in order to implement a model which allows the analysis of the improvement opportunities as a result of collaborative practices between the different echelons in the supply chain. SCs have joint
areas of interests, where collaboration agreements foster a win-win relationship between all the involved parties. Thus, the final aim of this paper is to simulate the behavior of supply chains using collaborative practices and support the assertion that the usage of these practices helps to improve the efficiency in the supply chain management.
Methodology
One of the most common ways to deal with simulation models is system dynamics which is not intended to be employed as a forecasting tool, but rather a learning means through which analysis of policy decision making can be reviewed.
In this regard, the chosen collaborative alternatives are the Vendor Management Inventory (VMI) and Electronic Point of Sales (EPOS). The brief idea behind VMI is that the upstream partner takes over all replenishment decisions of the downstream partner, while the main property of EPOS systems is that the whole SC has access to data about current sales to the end consumer The software tool employed for this project is Vensim ® due to its appropriate combination of system dynamics concepts and the simulation of discrete events to represent the supply chain´s events and uncertainties in detail.
Results and Conclusions
Three different scenarios were performed according to three different possibilities (traditional, VMI, and EPOS), proving all of them satisfactory responses to the purpose for which they were created. Indeed, it could be established that the usage of collaborative practices betters supply chain management.
As observed, the benefits do not only include a reduction in the supply chain inventories but also an increased service level, reducing the total amount of backlogged orders while boosting customer satisfaction.
Consequently, SC collaboration has been proven to be a reliable and helpful strategy which allows an improvement in the company operation´s deployment both at strategic and tactical level in order
to overcome the new and ever-more-changing requirements of demand.